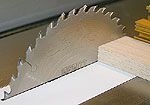 |
The Super-GeneralTM blade will make your table saw work better than ever.
Click image to enlarge |
Infinity Tools Super-GeneralTM Combination Blade
A new way to make table saw blades slick and tough
Text & Photos by Tom Hintz
Infinity Tools has once again strayed outside the box of conventional thinking with the release of their new line of saw blades. Rather than simply follow the crowd and apply some form of TeflonTM to their blades, Infinity looked at how other industries protected and improved metal components. Notable among these was the automotive industry where electroless nickel coatings on brake, transmission and steering components improved their performance and durability enough to help manufacturers offer longer warranty periods.
The result of Infinity's research is their innovative "Nickel ArmorTM " coating that enhances all of their new table saw blades.
Initial Impressions
The Infinity Super-GeneralTM has a distinctive shine to it, thanks to the Nickel Armor coating. Closer inspection shows high-quality laser cutting of the body, which is eventually given the Nickel Armor coating.
Inspecting the C4 micrograin carbide teeth reveals precise, finely ground surfaces that produce very sharp, long-lasting edges. The brazing which secures the individual teeth to the body is very cleanly done with no gaps or porosity noted.
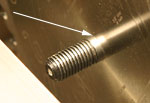 |
The center hole is perfectly sized and fits the arbor snugly, as it should.
Click image to enlarge |
An important but seldom checked feature of saw blades is the 5/8"-diameter center hole. Too often, we see upset edges surrounding the arbor hole and a slightly oversize diameter. Accurately forming and sizing the arbor hole, as on the Infinity Super-GeneralTM blades is more labor intensive but produces a blade that runs extremely true with virtually no radial deviations because it fits the arbor very closely.
To insure quality, Infinity does all of the design and development in house and then has their blades custom made to their exacting specifications in Italy. You may be surprised at how many of the best blades are actually made in Italy by very talented craftsmen using state of the art equipment.
In-House Design - Italian Manufacturing
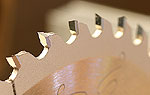 |
Infinity's in-house design combines the best of the Alternate Top Bevel design with top-quality C4 carbide teeth, meticulously machined to their stringent specifications.
Click image to enlarge |
The Infinity Super-GeneralTM is a 10"-diameter, 1/8"-kerf, 40-tooth combination blade tipped with super fine C4 micrograin carbide, known for its ability to take and maintain an exceptionally fine cutting edge. The teeth have an 18-degree hook angle and a 20-degree Alternate Top Bevel.
The blades body is precisely cut by an industrial, computer-controlled laser. All saw blades generate some heat while cutting that could distort the outer edge. To control even small distortions, the Infinity Super-GeneralTM has 4 laser-cut expansion reliefs spaced equally around its edge just below gullet level.
The laser also cuts 8 anti-vibration slots around the body, which dampen harmonics and absorb normally occurring vibrations that could lessen cut quality if left unchecked. The anti-vibration slots appear oddly shaped but are scientifically designed for maximum effectiveness under a wide range of cutting conditions.
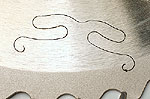 |
Laser cut anti-vibration slots keep the blade cutting smoothly.
Click image to enlarge |
Look closely at the anti-vibration slots you notice they are extremely narrow. That is because they are cut in one pass and show how small the actual width of the laser beam is.
A final step in tooth preparation is grinding a miniscule but important 0.005" side clearance that Infinity tells NewWoodworker.com produces a cleaner cut. This tiny amount of side clearance keeps each tooth in contact with the wood longer, performing a planning cut that essentially polishes the cut edge.
The all-important grinding of the carbide teeth is performed on a C.N.C. machine center that uses a 100% oil coolant. This high-pressure oil bath keeps the diamond wheel free of debris and produces a mirror finish surface.
Nickel Armor Coating
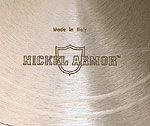 |
The nickel coating gives these blades a distinctive shine that resists buildup and cannot contaminate the wood.
Click image to enlarge |
Infinity chose to use the Nickel Armor coating on their new saw blades rather than one of the many forms of TeflonTM applied by many other manufacturers. Nickel coating is commonly used in manufacturing because of the high level of lubricity it adds to a part along with an equally substantial corrosion resistance.
Another plus to nickel coating is how tough it is. The plating process forms a tight bond that is highly abrasion resistant. This means that even in the harsh environment of cutting wood, there is nothing to transfer to the wood.
If there is a down side to this Nickel Armor coating, I have not been able to find it.
In The Shop
The close-fitting arbor hole in the Infinity Super-GeneralTM requires keeping the blade perpendicular to the arbor when slipping it into position. With the blade fully on the arbor there is no perceptible radial play between it and the shaft which translates into very smooth operation, as would be discovered as soon as the saw was started.
After completing installation, I checked the blade parallelism to the miter slot and the fence alignment. Both are routinely checked prior to testing a blade to be sure they do not influence the blades' performance.
Alignment of the saw itself is always important for performance and safety but with the closely machined tooth side clearance an out-of-line saw could induce scorching of the cut edge sooner than anticipated.
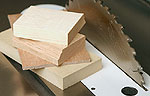 |
No matter what we cut, the Infinity blade left clean, smooth edges.
Click image to enlarge |
The Infinity Super-GeneralTM remained in my Jet contractor saw and was used for all cuts that came along in addition to the series of test cuts normally made when reviewing a saw blade. In all cases, the Infinity Super-GeneralTM performed flawlessly.
The first test I subject blades to is long rips in hardwood. These long cuts generate normal heat levels and allow feeling changes in how the blade cuts as the factory-fresh cutting edges go through the initial stages of wear. I have seen the performance of super-sharp blades slow quickly when the fine cutting edge, often surprisingly thin along the tooth edge, is beaten down a little. The Infinity Super-GeneralTM performed well in the rip tests, losing very little sharpness that meant virtually no increase in push-through effort or reduction in cutting speed.
The cuts were very smooth and the edges showed no chipping, even in hardwood veneer plywood. Cutting across the surface grain of 5 mm Luaun plywood yielded very clean cuts, something that has always been difficult to do.
Miter cuts at various angles felt secure with less tendency for the wood to move on the miter gauge fence. This appears to be due to the ease with which the Infinity Super-GeneralTM slices through the wood, which reduces the forces the blade exerts on the wood.
To test the Nickel Armor plating, sap-heavy pine was ripped repeatedly. Where other blades quickly developed buildup, the Infinity Super-GeneralTM resisted very well. There was a small amount of buildup noticed but it was easily removed. It appears the Nickel Armor substantially reduces the "grip" sap and other common buildup substances can get on the blades surface.
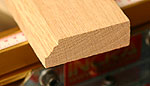 |
I cut this oak with the Super-GeneralTM exiting through the routed pattern. Notice how clean and chip-free the edge is, even on the fragile, sharp corners of the profile.
Click image to enlarge |
Resistance to buildup is an important factor in saw blade survival. Keeping the blade clean prevents harmful heat buildup which allows it to cut cleaner and stay sharp longer. The Infinity Super-GeneralTM aces this part of the testing easily.
Conclusions
With a price of only $89.90, (12-2-2004) the Infinity Super-GeneralTM blade (#010-040) is a very good value, in addition to being a top-quality performer in the shop.
The combination of Infinitys' innovative design using top quality materials and the Nickel Armor coating mean the Infinity Super-GeneralTM will last a long time with normal care. This is an important point for most of us who operate our shops on limited budgets.
When you need a new table saw blade, check out the offerings from Infinity Tools. In addition to the Super-GeneralTM, they offer a full range of blade designs to meet all of your woodshop needs. All of the Infinity blades are made with the same quality materials, superior manufacturing and feature their Nickel Armor plating used on the Super-GeneralTM reviewed here.
Infinity Tools products are only available direct from them. Visit the Infinity Tools website at www.infinitytools.com or call them at 1-877-872-2487.
Do you have a comment about this page? - Email Me!
Back to the Tool Reviews List
|