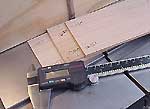 |
Anytime I need a digital caliper to find deviations in a saw cut, I consider that blade to be the best. Such is the Timber Wolf band saw blade.
Click image to enlarge |
Timber Wolf Band Saw Blades
When "Too good to be true," turns out to be true
Text & photos by Tom Hintz
Like many of you, I have struggled with a smaller (read "affordable") band saw, trying to get it to re-saw like its big brothers. In addition, like many of you, I have tried the rounded fences, setting fences crooked to the blade, using inappropriate blade designs for the job and even doing a little re-sawing dance when nobody was looking. The result of these increasingly bizarre efforts was re-saw cuts in smaller material that were occasionally acceptable. However, when stock width exceeded a couple inches, particularly hardwoods, the cuts often resembled a topographical relief map of the Kentucky hill country. This scenery is beautiful in person, but terrible on an expensive piece of wood.
While searching for a budget-friendly answer to my re-sawing woes, I noticed that even the more fortunate woodworkers with 14 and 16-inch band saws were having similar problems, often to a lesser degree, but they still were not satisfied. Size on it's own is apparently not the answer.
About a year ago, I began noticing what appeared to be exaggerated claims regarding the capabilities of Timber Wolf band saw blades. For a while, I resisted the temptation to run out and buy one, not wanting to be suckered in by what was sounding increasingly like exaggerated claims of near-unbelievable performance.
Recently, while touring the Charlotte woodworkers show, in the midst of the over-amplified hucksters who mechanically rattled off occasionally wild overstatements regarding their product's capabilities and equally overstated claims about competitors inadequacies, was an older gentleman calmly explaining how Timber Wolf band saw blades worked. As he talked, he was demonstrating those capabilities in a simple, straightforward manner. After listening to this island of sincerity, I thought there just might be something to these Timber Wolf blades after all.
The next day, I bought one.
My local store didn't have the ½"-wide Timber Wolf blade I wanted, so I settled on a 3/8"-wide blade with a tooth count of 6-per-inch. It wasn't the re-saw blade I wanted, but it would handle the majority of the jobs I normally do on my band saw.
The next morning I installed the new Timber Wolf blade in my four-year-old Craftsman 12" band saw. You know, the saw the always-shrill Craftsman-bashers claim won't cut straight regardless of what blade is used.
The Test
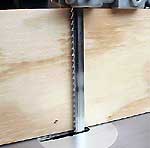 |
I installed the silicon steel Timber Wolf blade according to the instructions. The amount of tension needed was drastically less than with any other blade I have tried!
Click image to enlarge |
I decided to subject the Timber Wolf blade to an official NewWoodworker.com test under the following admittedly questionable conditions:
Facility - The official NewWoodworker.com Test Lab (Looks oddly like my half of the garage)
Equipment - Craftsman 12-inch band saw - lots of miles on it, but taken care of (Sorry, I didn't amass 14 band saws for the test, you'll have to settle for the one I bought)
Blade selection - The Timber Wolf 3/8", 6 T.P.I., 80" (My entire Timber Wolf inventory at the moment)
Test Material - Oak (Scraps discovered under my bench)
Test Preparation
Getting ready for this test began with adjusting the blade according to the Timber Wolf instructions printed on the decidedly non-flashy card/label stapled around the coiled blade. After following the Timber Wolf procedure, I found the indicator on my saw showed far less tension than recommended for any other blade previously used on the test machine. According to the gentleman at the show, the reduced tension requirement is due to the use of silicon steel to make the blades.
I made sure the blade guides were properly adjusted, the blade centered on the wheels and that the table was level to the blade. I also blew off the dust so you wouldn't see it in the pictures.
I built a 3"-tall fence that was almost 90-degrees to the table surface. Actually, I thought it was 90-degrees, but as you will see, the test results indicated otherwise. The fence was set approximately (eyeballed actually) 1/8" from the Timber Wolf blade and squared (horizontally) with the edge of the table.
The Test
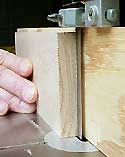 |
Even with a "slapped-together" fence and pushing the stock through by hand, the cuts were nearly perfect. The amount of error appears to be the identical as the amount the fence is out-of-line.
Click image to enlarge |
A 3'-wide by 8"-long by ¾"-thick piece of oak was selected for the first (learning) cuts. Four slices were made and the pieces laid out on the cast iron surface of my table saw. The initial analysis (I rubbed my finger across the pieces) showed all three slabs were the same thickness. They also showed no evidence of the "hill and dale" features often seen with this saw previously.
Next, a 3"-wide by 24"-long by ¾"-thick piece of oak was sliced three times (I needed three pieces for a project) with what appeared to be the same results. There was no visible variation in thickness across the three pieces again, tested with the same finger rub as the first test.
Qualifying the Results
Realizing that I had never seen an actual straight re-saw cut before, I thought perhaps more scientific testing was in order.
I marked all four corners of each piece, roughly ½' in from the ends and measured each of these spots with a good digital calipers, the only real scientific instrument I have. I even went around each piece twice just to see if I came up with the same figures more than once. I did.
The thinnest section noted was 0.134" and the thickest, 0.154." These measurements also suggested that my fence was probably not exactly 90-degrees to the table.
The bottom edges of all the pieces had a thickness range of 0.134" to 0.140" while the upper edges ranged from 0.151" to 0.154."
If these pieces had been cut on a milling machine, we'd have a problem. Considering they were cut on a band saw with me sliding them down a rigged up fence by hand, I think we can safely assume the blade is cutting straight and that my hasty fence construction is slightly out of whack.
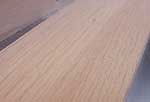 |
The surface left by the blade after cutting was easily sanded smooth with an old 220-grit disc in my ROS.
Click image to enlarge |
I also noted that the fine ridges left on the freshly cut surface were small enough to disappear almost instantly under the influences of my random orbital sander equipped with a well-used piece of 220-grit paper.
Conclusions
The Timber Wolf blade I bought did exactly what it was supposed to do, and more. Though not designed as a re-saw blade, it re-sawed perfectly. As would be expected, this blade handled more common straight and curved cuts effortlessly; leaving a surface that required little sanding to prepare for finishing.
The fact that the Timber Wolf blade drastically improved the performance of my band saw is remarkable, and may be a little disconcerting to the manufacturers of the higher-dollar machines known for their re-sawing prowess. What if too many woodworkers find out their re-sawing problems might be solved by a new blade rather than a new machine?
Now, if Timber Wolf could figure out how to make their blades increase vertical re-saw capacity, there could be real trouble in the band saw retailing world.
Does this sub-scientific test indicate Timber Wolf band saw blades will solve all your problems? I have no way of knowing, but the near perfect performance under my less than perfect conditions tells me what band saw blades I will buy in the future.
If you are having troubles relating to cut performance on your band saw and you have not been using Timber Wolf blades, I think trying one before replacing the machine is a very wise investment.
Visit the Timberwolf site - www.suffolkmachinery.com
Do you have a comment about this page? - Email Me!
Back to the Tool Review List
|