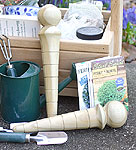 |
Dibbles are fast and easy to make but will impress your favorite gardener.
Click image to enlarge |
Turning a Dibble
A fun, simple project for the gardener in your life
Text & Photos by Tom Hintz
A Dibble (also called a Dibbler) is a simple tool used by gardeners to create holes in soil for planting seeds and small plants. The base design includes a ball-shaped handle, a flare and a taper with a series of 6 markings at 1" intervals that serve as a depth gauge. Modifying the Dibble with your own ideas or to fit your favorite gardeners needs is simple.
Material
Virtually any type of wood can be used to make a Dibble. Most gardeners keep their Dibble in a tool kit that is stored out of the elements when not in use. Because the Dibble is quick and easy to turn, making several to keep a gardener supplied for years to come can be done in a single afternoon.
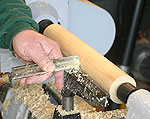 |
After making a few Dibbles, rounding the initial cylinder takes almost as long as the rest of the turning!
Click image to enlarge |
The Dibble made for this story was turned from a piece of scrap
pressure treated (non-arsenic chemicals) wood. Obvious alternatives include any wood with weather-resistant properties such as cypress or cedar. However, any piece of scrap that is large enough will do nicely and will make a Dibble that will last a season or longer.
The finished Dibble is about 9"-long with a maximum diameter of 2". Using a blank 2 ¼" to 2 ½"-square and 12"-long leaves more than enough scrap at either end to make turning this project between centers safe.
Rounding and Sizing
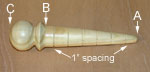 |
Turning sizing grooves at these points on the blank makes turning the Dibble easier and assure the correct proportions.
Click image to enlarge |
Begin by turning the blank to a 2 1/8"-diameter cylinder. I like to turn Dibbles with the small end at the tailstock because forming the taper feels more natural to me in that direction. The layout as described in this story refers to that orientation.
Make pencil lines around the blank 1" (A), 7 ½" (B) and 10 ½" (C), measured from the right end of the blank. These dimensions leave about 1" of scrap at the tailstock. Use a parting tool to turn a sizing groove down to ¾"-diameter at the A mark (left to right), 1 ½"-diameter at the B line and 1"-diameter at the C mark. These grooves mark the main transition points.
Shaping
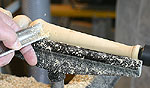 |
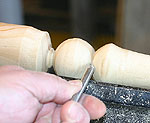 |
(Top) Working in the taper is easier if you alternate with shaping the ball end. (Bottom)
Click images to enlarge |
Rough in the taper between the A & B marks, leaving it slightly oversize for now. As material is removed, especially at the B mark, the handle and flare area gets in the way. It is easiest to use a spindle gouge to begin roughing in the ball handle and the flare below it at this time also. Turning a rough cove in the left-side waste creates room for turning the top of the ball.
Alternate between shaping the taper and handle features until both areas are close to finished size. I leave at least ¾" of material at the cutoff points for now to maintain stability of the piece during the final turning and sanding.
When all of the shapes are turned to size, sand all surfaces down to 150-grit.
Depth Indicator Lines
With the lathe off, lay out lines 1" apart, starting at the point of the taper. If the handle features were located properly, there should be room for 6 markings below the handle flare. Turn the lathe on and cut V-
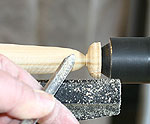 |
Work both ends toward finished size but leaving 1/4" to 3/8" of material to support the piece during sanding and finishing.
Click image to enlarge |
grooves about 1/16"-deep and 1 1/16"-wide at the layout lines.
Keep in mind that the lines need only be easily visible. Cutting them too deep or wide serves no purpose other than creating a place to catch more dirt.
Complete Turning
Finish sand all of the surfaces down to at least 220-grit, being careful around the depth lines. Sand any frayed grain around the lines but do not round their edges over.
Turn the ends down to their final shapes, leaving ¼" to 3/8" of stock to support the piece during finishing.
Applying a Finish
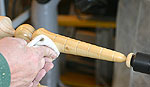 |
Though fine without finish, I like to "burn on" a little Hut turning wax to give the Dibble a nicer look.
Click image to enlarge |
Though Dibbles need not be finished, I like applying a simple "burned-in" wax finish (Hut stick) to improve the appearance and give it a little protection.
Apply the finish according to the manufacturers instructions, down to the cutoff areas at either end to minimize the amount of touch-up required later.
Part the Dibble Off
Carefully part the Dibble from the waste. Use a sharp utility knife or chisel to trim any remaining waste before hand sanding the ends smooth. Be sure to round the end of the taper rather than forming a point that will just break off in use.
Apply finish to the bare wood at either end and your Dibble is ready to be presented to your favorite gardener!
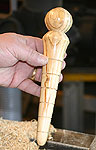 |
Before you know it, your first Dibble is done!
Click image to enlarge |
Options
This is an easy project to turn and equally simple to modify to fit your gardeners wants or needs.
The 6" range of depth is most common but the tapered section can be made longer to accommodate special planting needs. The ball-style handle is comfortable to use but could be augmented with grooves to increase grip or shaped differently if the user has special needs or just likes another form.
The key is to have fun, practice the turning skills used and be creative.
|